
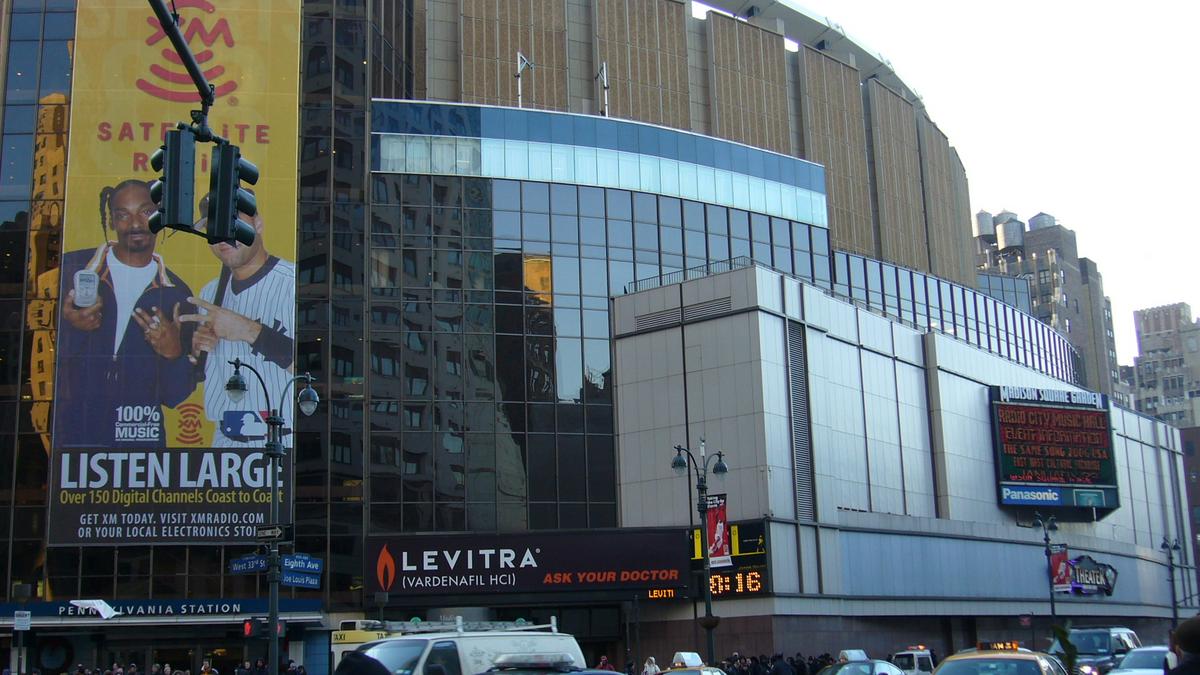
#GAARDNER DENVER HOLDINGS SPIN IOFF SOFTWARE#
Because this picking system proved quite successful in handling the large-volume of 80,000 different parts - mostly small components - in the DC, Gardner Denver asked Remstar to again design and build picking systems to accommodate its new warehouse needs in its Sedalia and Quincy manufacturing plants.As the industry leader in small-parts handling, Remstar is capable of integrating a holistic systems solution to inventory management, incorporating horizontal carousels, vertical carousels, vertical lift modules, inventory management software and put-to-light/pick-to-light systems. The DC would receive an order from a customer for aftermarket parts, the picking carousels would house them and the orders would then be picked and shipped out to its customers. This was now to be expanded and integrated to handle both assembly parts inventory and aftermarket parts warehousing and distribution within the same system.The companys Memphis DC had automated picking carousels previously designed and built by Remstar International that were used strictly to fill aftermarket orders. Each of the plants already maintained a warehouse for supplying parts needed for assembly. Both were exclusively production plants, Sedalia manufacturing rotary screw and industrial blowers, and Quincy manufacturing reciprocating compressors and pump products. Instead of maintaining duplicate sets of 80,000-plus SKUs in inventory, it could have just one set of SKUs for each of the two manufacturing sites.The two plants designated to absorb the Memphis DC aftermarket inventory and distribution activities were the companys Sedalia, Missouri facility and Quincy, Illinois facility. This was essentially a change in the companys distribution model - Gardner Denver determined that it could reduce its inventory costs significantly by combining its aftermarket parts fulfillment with its production warehousing at two of the companys manufacturing facilities. The decision was made to move its aftermarket parts fulfillment to the plants that were responsible for manufacturing those products, and to close the Memphis DC. Gardner Denver conducted an assessment of its assembly parts needs for its manufacturing facilities, its aftermarket parts needs, and lead times required for managing its inventory level. There were potentially sizable benefits, however, to having the companys aftermarket distribution coming from the production facilities themselves, where the parts were actually being manufactured.

This system had been utilized for the past 20 to 25 years. The company would manufacture aftermarket parts in its other plants, ship the parts to Memphis where they would be inventoried and then sent out to customers. Making the Switch from Dedicated DC to Integrated WarehouseGardner Denver maintained a dedicated aftermarket distribution warehouse in Memphis, Tennessee which handled its aftermarket parts fulfillment for the domestic manufactured compressor, blower and pump products. The company has a tremendous installed base of equipment in manufacturing plants throughout the world, going back almost 150 years when Robert Gardner provided the first effective speed controls for steam engines back in 1859.

Its products and engineered solutions are sold through multi-channel, worldwide distribution systems and are used for applications in virtually every market sector, ranging from industrial movement to environmental processes, to healthcare applications and energy production. The company is a leading global manufacturer of highly engineered reciprocating, rotary and vane compressors, liquid ring pumps and blowers for various industrial and transportation applications, pumps used in the petroleum and industrial markets, and other fluid transfer equipment serving the chemical, petroleum, and food industries. That is unless you are Gardner Denver, Inc., who in the fall of 2005 completed the integration of its large, dedicated aftermarket fulfillment center into two of the companys production facilities, pulling off the transition in record time and without missing a logistics beat.Gardner Denver builds large pumps, compressors and blowers for industrial use. But, integrate into that system a full-scale aftermarket fulfillment distribution center with 80,000 additional active SKUs needing to be processed simultaneously, and you have the recipe for a potential logistics meltdown. SeptemFor any large industrial manufacturer handling 13,000 SKUs in their assembly parts warehouse, it is no small organizational challenge to keep production requirements satisfied without a hitch. It upgraded its distribution center to a picking system by Remstar. Gardner Denver builds large pumps, compressors and blowers for industrial use.
